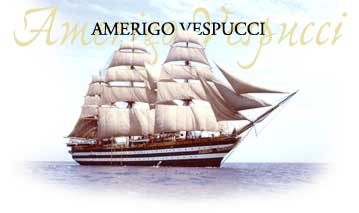
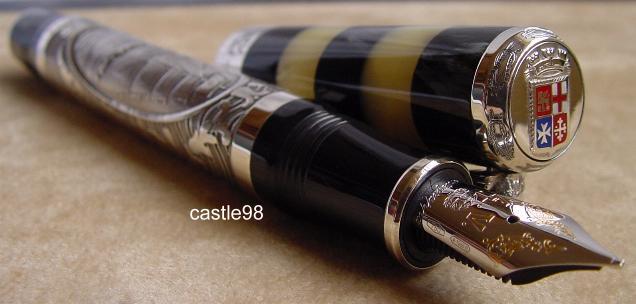
Overview
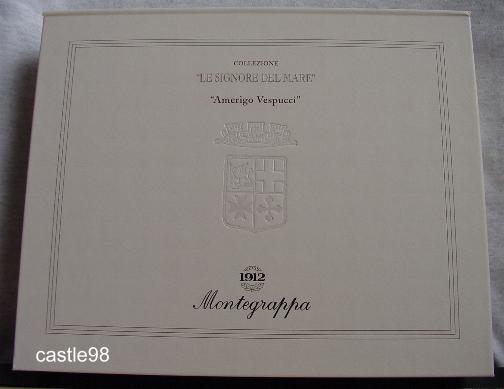
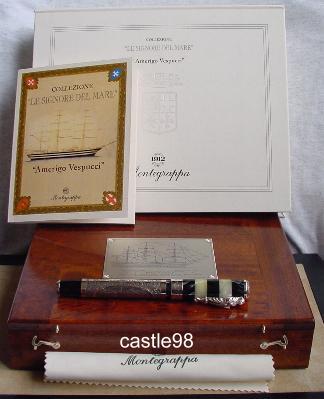
Great presentation
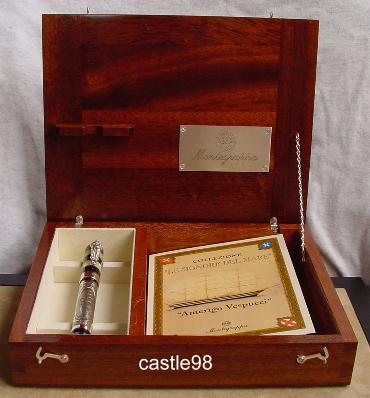
Wooden box
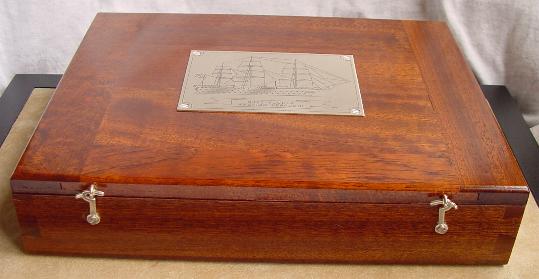
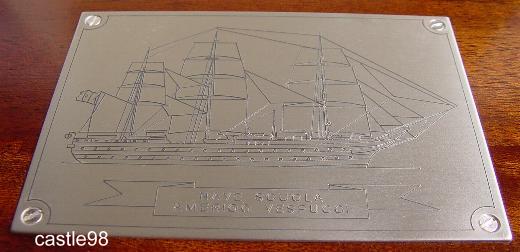
THE
VESPUCCI FOUNTAIN PEN
Towards the end of the fifties, a modern US Navy
aircraft carrier sailing in the Atlantic encountered a magnificent sailing
ship with its keel painted in black and white horizontal stripes and
majestic rigging, travelling with its sails fully open. "What ship is
this?" asked the Americans in code Q, with a series of flashes of their
message light. "Vespucci of the Italian Navy" was the reply.
"You're the finest ship in the sea" declared the US aircraft
carrier in admiration, as it sailed off with its crew lined up on deck as on
a parade of honour: This episode, which has become something of a legend,
gives an idea of the fascination this splendid vessel is able to exert. It
was launched on 22nd February 1931, and for the last seventy years has been
used as a training ship by the Italian Navy, offering an essential
contribution to the training of the future officers emerging from the Naval
Academy of Livorno.

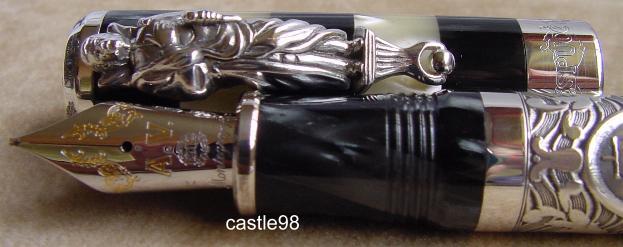
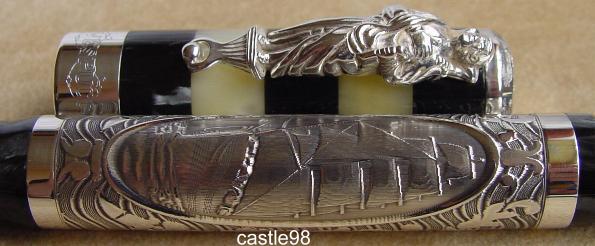
The Amerigo Vespucci was built in the
Castellammare di Stabia shipyard to a design by Lieutenant Colonel Francesco
Rotundi of the naval engineering unit, and although it has a diesel electric
engine with a power output of 2000 Hp, its fundamentally a sailing ship,
with lines inspired by the nineteenth century vessels, with three masts and
a bowsprit, square sails, staysail and jib. It has a displacement of 4,100
tons, an overall length of 101 metres, maximum breadth of 15.5 metres and a
sail area of approximately 3,000 square metres. Unmistakable due to the
elegant black and white stripes of the keel and the magnificent ochre
coloured rigging, with the mainsail towering more than 55 metres high, the
Vespucci catches everybody’s attention, whether moored or at sea, with its
beauty, and attracts long queues of visitors to the moorings, prepared to
put up with long waiting times to come aboard. To have an idea of the amount
of work that has to be done to move a ship of this kina; just consider that
as well as the students that rotate on board each year; there’s a crew of
no less than 267, and around 50 kilometres of cables, ropes and sheets are
needed to adjust the sails. On board this university of the sea, the cadets
from the Naval Academy of Livorno complete their studies by practising all
the disciplines of sailing and learning the science of navigation. An
intense, tiring and by no means easy life, but with the satisfaction of
knowing that you're serving on the finest ship on the seas.
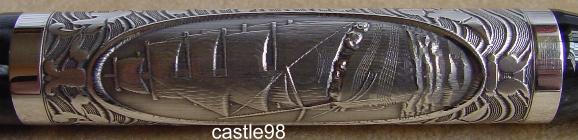
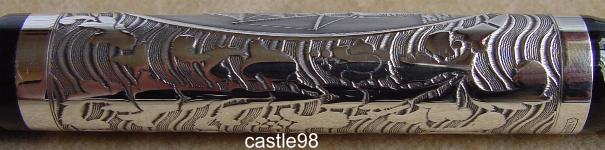
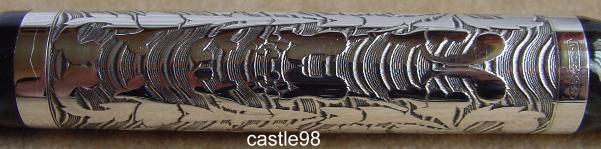
It was therefore inevitable that Montegrappa 1912
decided to dedicate to this vessel the first fountain pen in its new
collection of writing instruments known as 'Le Signore del Mare" (The
Ladies of the Sea), which is now being launched on completion of a highly
ambitious and committed design study and which, after the Vespucci, will be
expanded with the finest and most beautiful sailing ships in the Italian
Navy.
With its tradition of the finest craftsmanship and
its perfect control of the most refined jewellery techniques, only
Montegrappa could have accepted the challenge of faithfully reproducing the
lines of these magnificent and instantly recognisable ships, so complex and
rich in essential details, miniaturised in the body of a fountain pen.
The sterling silver version, produced in 1931
examples, shows the same image of the ship, but in low-relief. The pearlized
celluloid cap, with its refined black and white stripes, recalls the most
outstanding feature of the keel.
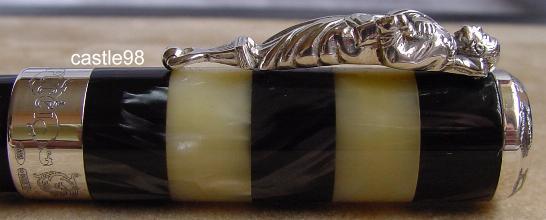
At the top of the cap is the so-called
'jack", or bowsprit flag, in sterling silver or 18 carat gold, with the
manual application of the enamel.
The presence of this square flag, which unites the
ensigns of the four Maritime Republics and is always flown at the bow when
the Italian ships are moored in the harbour or at anchor, bears witness to
the official nature of this collection, which obtained the approval of the
General Staff of the Italian Navy with letter no. 80065363 of 6th
August 2000.
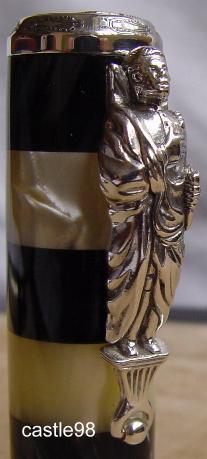
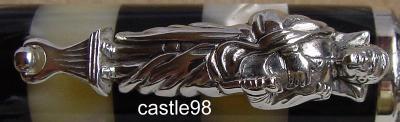
The clip, in sterling silver is another authentic
work of the jewellers art, taking the form of a miniature reproduction of
the figurehead, or bow statue, which shows the great Tuscan navigator
Amerigo Vespucci whose name the ship bears. The sterling silver adds the
final touch to the cap is engraved with the name of the ship.
The 18 carat gold; partially platinum-plated nib
is engraved with the monogram AV, adorned with the typical graphic
flourishes used as an elegant support to the figurehead as the bow of the
vessel. The ink feeder is hand turned ebonite, which guarantees a consistent
and flawless ink flow.
The feeding system is by the traditional piston
method, with a high capacity ink reservoir.
This fountain pen, which, as an imitation of the
ship to which is dedicated, aspires to be the finest in the world, is
completed by its presentation case.
It is an absolutely genuine reproduction of a
ship’s box designed to contain navigation instruments. An indispensable,
precious accessory, manufactured specially in seasoned mahogany.
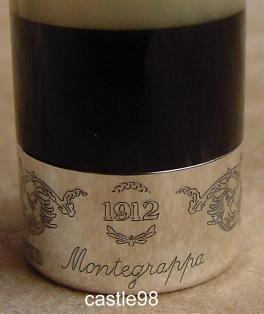
Front and Back of the Cap
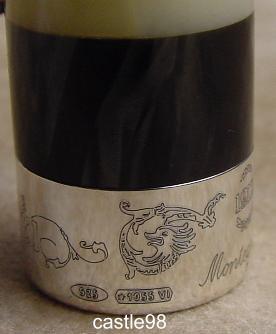
Both sides of the Cap
“Amerigo Vespucci" fountain pen
is manufactured deploying precious materials and jewellery techniques, such
as low relief engraving and vitreous enamelling for the pens barrel, and
hand-enhanced die casting for the clip. Exclusive techniques that make
Montegrappa writing instruments unique and unequalled.
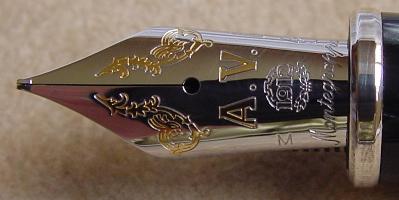
Solid gold 18K nib
LOW RELIEF ENGRAVING
Montegrappa a name invariably
associated with whenever the art of low relief engraving is mentioned.
Unique and the only pen manufacturer to deploy this technique, in 1992
Montegrappa produced the 80th Anniversary pen from which much applause and
admiration was received from the general public as well as other
manufacturers.
Beginning with the subject of design, a
pattern is mapped out in the special CAD/CAM System.
Thereafter; the designing process
becomes the center of concentration as the image to be etched, has to form a
continuous pattern around the tube. It is at this stage that the programming
of the CAD/CAM plays the crucial and vital role in this technique. Sometimes
taking up to months, this tedious and complex process that requires
designing, drawing and test-etching is repeated to arrive at the finalised
pattern. Any minute mismatching of the pattern can result in disastrous and
costly consequences.
Matched to perfection, the meeting
point where the engraving starts and ends can sometimes be oblivious even to
an expert.
To deploy the special technique of low
relief engraving, a special CAD/CAM System is used to perform all the
functions of 2 dimensional engine turning and in addition generates low
relief surfaces whereby small amounts of' metal is carved away whilst
cutting very fine lines which vary in depth.
The 3-D image is recessed out of the
surface in a finely scanned pattern.
It is not necessary for the path of the tool to be straight in the X-axis,
though for most Low Relief a straight line is usually chosen.
Precision engineering and consistent
quality checks of the end product is required to ensure consistency in the
production. With the result of a product only of the finest finishing and
quality that can be expected from a process and technique so refine, even
"Michael Angelo" would be jealous of …Which is why, Montegrappa
makes writing a privilege. . . . “The
Privilege Of A Lifetime”.
ENAMELLING
An ancient art that has been preserved
for generations since the VI century B. C. This painstaking process was and
is still used by silver and goldsmiths as a vitreous material for decoration
to enhance their work of art.
Appreciated for its wide variety of
chromatic ranges and its enduring ability of perfect preservation. The use
of enamel has left its mark in history in the periods of greater artistic
fertility, from the Egyptians to the Middle ages and the Renaissance to the
XIX Century. For greater visual presentation, two effects were created. “A
giorno" meaning "day", results in the enamel being
translucent allowing the background to be seen, and “A notte” meaning
"night", results in an opaque finish with the latter technique
being most commonly used.
Enamel is composed of finely grind
crystal, coloured by metallic oxides that generally leave it translucent
which can also be opaque by adding a certain quantity of stain oxides.
The object that one wishes to enamel
has to be endowed with special features in order to be processed.
To create the dramatic colour effect
and contrast between dark and light shades, the lower surface is
"engine turned" or etched. The edges of the recess to be filled
with enamel needs to be chamfered to allow the intricate application as well
as the heating process to be conducted.
The surface to be enamelled have to be of
consistent thickness to withstand the extreme temperatures of this process.
In between multiple coats of enamel
being applied with a brush, the object is heated at temperatures between 750
to 830° C until the enamel melts and fuses itself to the object.
This time consuming and tedious process
is repeated for each different colour used until the completion of the
design is achieved.
Using a special tool made of
carborundum, the finished design is then filed to obtain a perfectly smooth
surface and polished with brushes of felt and pumice. Ultimately to protect
the finished masterpiece, the whole process is repeated with a thin layer of
transparent enamel.
The incredulous patience needed for
this tedious, time consuming, labour intensive and intricate work of art,
showcases the superlative
creativity of craftsmanship embodied in a masterpiece to be treasured for
generations.
Simply
Beautiful!!
HAND-ENHANCED DIE-CASTING
“Die-casting" or sometimes
referred to as "lost waxed casting" has been a process used
extensively since the fifth century the process has changed very little
since that time. The multiple stages of work involved in die casting is
mountainous that one would rarely consider venturing into this business if
not for the field of
specialisation.
To begin, a hand carving of a
three-dimensional sculpture, like of the pen is encased in a plastic
"dough" which dries to a rubberlike mould. Then a zic-zac incision
is made at the side and the sculpture is removed.
With a special vacuum wax injection
machine, the air is 'sucked and melted wax is injected into the mould,
creating an exact replica of the sculpture. After hardening, multiple
replicas are affixed to a "tree" at a time , encased in plaster
and heated in an special oven. The wax melts and drains from a hole in the
cast at 180° Celsius before it is hardened at temperatures as high as 750°
Celsius. Each plaster cast can only be used once. Thereafter; cooling to 600°
Celsius, molten silver or gold is poured the plaster cast and left to sit
for 15 minutes and then plunged into water. The process cracks the plaster
exposing the sculptures.
At this point, the experience of a
skilled craftsman takes centre stage and small details which might have been
lost in the casting process are redefined by hand.
The 'antiquing" and polishing of
the sculpture to its refined look, forms the final stages of the die-casting
process. It is with great anticipation when each piece of die-cast pen goes
through a long and tiresome process to unveil a timeless art deserving of
such acclamation and a place in the showcase amongst other collectibles.
|